fixed tub Ordinary round tub plating Ordinary round tub plating Electroplating rotary tub is among the…
Plating
Metal plating, types and execution method
In general, it can be said that electroplating is an anti-corrosion method and coating that increases the resistance of metals. There are different types of electroplating, including iron, nickel, silver, etc.
Stay with us to learn more about the process of plating metals, the purposes of plating and the method of its implementation.
Do you need plating services?
We have a better offer for you!
- Cheaper cost than electroplating
- Several times more resistant to corrosion
- Can be done on small and large parts
- Alternative to nickel, chrome and galvanized plating
03145273010
What is electroplating?
Plating is the process of placing an anti-corrosion coating of metal on another metal by hydrolysis, which is usually done for many purposes, from corrosion prevention to decorative purposes.
Electroplating allows manufacturers to use inexpensive metals such as steel or zinc for appearance, protection, and other desired properties in the outer layer of metals. The surface used for electroplating can be of different materials such as metal, etc.
Plating is one of the metal coating methods. To learn about its various methods, the articleGet to know 7 methods of coating metalsread the
History of electroplating
Metal plating was first discovered by Luigi Brugnatelli in 1805, using an electroplating process for gold plating. However, his discovery went unnoticed because the French Academy of Sciences ignored him. But a few decades later, John Wright succeeded in using potassium cyanide as an electrolyte for gold and silver.
Elkington’s cousins later used potassium cyanide as an electrolyte in 1840 and succeeded in developing an electroplating method for gold and silver. They patented the electroplating and the method spread widely from England around the world.
Purposes and benefits of electroplating
In general, metal plating has the following advantages:
- Appearance beauty
- Protection of metal products
- Special surface properties
- Engineering or mechanical properties
- Hardening of the surface of the material
- Improve paint adhesion
- Soldering reinforcement
- Improve wearability of the piece
- Reduce friction
- Conductivity change
- Increase iron resistance to heat
- Also, the plating of various metals such as tin, zinc and iron makes food storage parts such as tin cans work in the best way.
Types of metal plating
There are different types of metal plating, in the following we will only give a brief explanation of iron plating and mention the names of other plating methods.
- Zinc plating
- Iron plating
- Cadmium plating
- Chrome plating
- Nickel plating
- Copper plating
- Silver plating
- Gold plating
Plating iron anti-corrosion coating
Iron plating is one of the plating methods that is several years old and there is still a demand for it. We know that iron reacts quickly when exposed to oxygen and causes its corrosion and rust. There are many methods to deal with metal rust, one of which is metal plating.
The method of metal plating
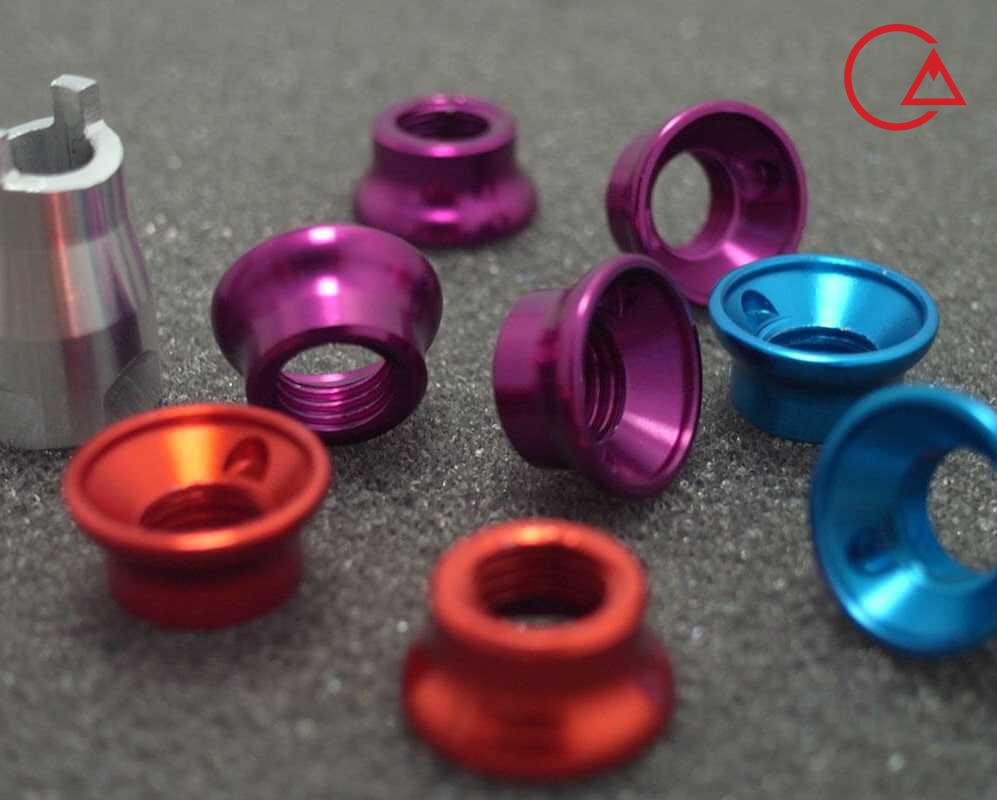
In the following, we will give more explanations regarding the steps of implementing the electroplating coating
The first step is pre-treatment or surface cleaning
The first step for iron plating is the preparation of its substrate. This is an important process aimed at removing all harmful contaminants such as greases and oils. In cases where there are welds, holes and other surface inconsistencies, fix them.
For preparation, you can use different cleaners, including acid cleaners such as hydrochloric acid, sulfuric acid, or alkaline cleaners such as carbonates, phosphates, etc.
The second step is to determine the effectiveness of the cleaning process
At this stage, you must ensure that the desired layer and surface are clean. For this, you can use water or a cloth to make sure the surface is clean by running water, or clean the desired surface with a cloth, if there is no trace of dirt and pollution, perform the electroplating process.
The third stage of the electroplating process
After ensuring the cleanliness of the surface, it is time to start plating the metals. For this you need a direct current source. Other materials include tank or (barrel), cathode, anode and suitable plating solution.
As soon as the electric current is turned on, the coating process begins. Before plating you have to consider variables for different metals. These variables include voltage level, temperature, immersion time, etc.
- Selection of electrolytes » There are various metals that can be used in electroplating. Some electrolytes include: bases, acids, metal salts, etc. When choosing the required electrolyte, you should consider things like corrosion, resistance, brightness or reflection, hardness, mechanical strength, malleability and wear resistance.
- Compounds » The compounds used in iron plating include sulfamate, sulfate, chloride, etc.
- Iron plating bath » Finally, plating is done by immersing the metal piece in a bath containing an acidified iron salt water solution. This solution consists of about 0.25 grams of alkali metal from mononaphthalene sulfonic acid condensate per liter.
What is fortic plating?
Fortic plating is a combination of plating and painting methods. In the fortic plating process, a piece of metal is placed in a water-based solution. In the desired water-based solution, there are colored grains.
After placing the metal in such a solution using a certain electric voltage, they lead to the absorption of the colored grains in the solution by the metal. It should be noted that in metal plating in this way, electric voltage is transferred to the metal and it is this voltage that causes the absorption of colored grains.
What is iron zinc?
Zinc-iron is an alloy of two metals zinc and iron. This is the result of zinc plating with the addition of an iron alloy. The iron content is between 0.3 and 0.1%. The purpose of producing such a product is to improve the properties of zinc. Plating on iron works with the underlying metal component to further strengthen and improve the properties of the base metal.
Why use zinc-iron plating?
One of the important advantages of applying a zinc-iron layer on a surface is to create an anti-corrosion coating and an anti-rust coating in metals. Since zinc has high resistance, we increase its resistance by 25 to 50% by alloying zinc and iron to cover metals.
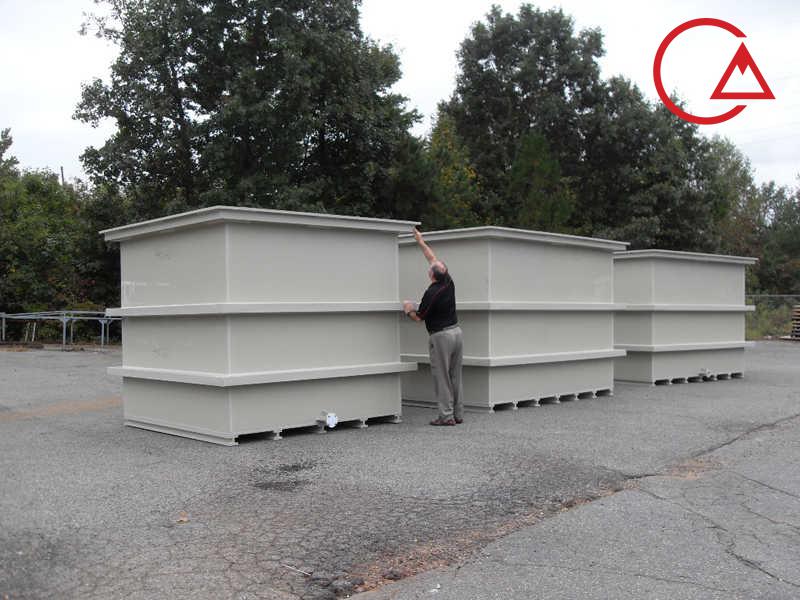
Advantages of plating on iron
Zinc and iron plating provides other advantages for the layer and substrate, which include:
- Good malleability
- Excellent surface appearance
- Uniform distribution on non-uniform and irregular components
- Excellent lubrication
- High difficulty level
- Resistance to salt spray more than 480 hours
Iron plating is an excellent choice for components intended for further fabrication operations such as coatings, paints, and waxes. This process also results in higher colorability of the final product.
For example, in the automotive industry, extreme black chromate coating is very popular. Overall, perhaps the most attractive feature of zinc-iron plating is its ability to produce a blacker part than can be achieved using zinc plating technology.
Conclusion
Electroplating, also known as electroplating, consists of depositing a thin layer of one metal on the surface of another metal, which is a type of metal plating. During metal plating, both metals are placed in an electrolytic solution.
The metal to be coated acts as the anode, while the coating metal acts as the cathode. Plating coating has very good corrosion resistance and can increase some mechanical properties of metal. Surface plating also creates an aesthetically pleasing appearance and makes it ideal for covering jewelry and ornaments.
Introduction to the electroplating process video
In the following video, first, the types of plating methods will be shown, and then you will see the metal plating process that you have studied throughout this article.
Frequently Asked Questions
What is metal plating?
Plating is the process of placing a metal coating on another metal by hydrolysis, which is usually done for many purposes, from corrosion prevention to decorative purposes.
Types of plating
There are different types of plating, such as zinc, nickel, silver, gold, etc. Additional explanations in the text of the article.
Plating coating implementation steps
Plating coating has different stages, the implementation stages and more explanations about each of them are available in the text of the article.
Advantages of plating metals
Metal plating has many advantages, for example, two things are mentioned, which are: protection against rust and corrosion of metals, higher colorability, etc. Other items in the article.
What is anodizing?
Anodizing is an electrochemical process that coats a metal surface with a decorative, durable, and corrosion -resistant anodic oxide…
Types of metal plating and their benefits!
Metal plating has many advantages for products made of metal and other materials. Plating is a…