- بال میل یا آسیاب های گلوله ای به استوانه هایی از جنس فولادی یا سرامیک گفته می شود که مشابه سیلندر می باشند و معمولا یک پوشش غیر فلزی از جنس سرامیک اطراف آن را برای جلوگیری از آلودگی های فلزی می پوشاند.
- بال میل ها به صورت افقی نصب می شوند و تا حدودی با گلوله های گرد فولادی و یا سرامیکی پر می شوند تا مواد سخت را به پودری نرم تبدیل کنند.
- بال میل یا آسیاب های گلوله ای به استوانه هایی از جنس فولادی یا سرامیک گفته می شود که مشابه سیلندر می باشند و معمولا یک پوشش غیر فلزی از جنس سرامیک اطراف آن را برای جلوگیری از آلودگی های فلزی می پوشاند.
- بال میل ها به صورت افقی نصب می شوند و تا حدودی با گلوله های گرد فولادی و یا سرامیکی پر می شوند تا مواد سخت را پودری نرم تبدیل کنند.
کاربرد بال میل
- بال میل کاربرد وسیعی در صنایع فرآوری مواد معدنی و شیمیایی داشته و در بخشهای خردایش نهایی و تولید پودرهای میکرونیزه بکار گرفته می شوند.
- به منظور تولید پودرهای میکرونیزه معمولاً این آسیابها در یک مدار بسته با سپراتورهای هوایی و یا کلاسیفایرهای هوایی و یا هیدروسیکلونها ، قرار می گیرند
- دستیابی به دانه بندی مناسب محصول آسیاب گلوله ای و میله ای دوار وابسته به مشخصات ابعادی و مکانیکی دستگاه و همچنین سختی و مشخصات مواد ورودی به آن است که لاجرم حصول نتیجه مطلوب را منوط به انتخاب صحیح و طراحی مناسب دستگاه می سازد
موارد مصرف
- سیمان
- کوارتز
- فلدسپار
- آهک
- کلسیت
- باریت
- روی
- مس
- طلا
- نقره
- سایر مواد معدنی مشابه
مزایای بال میل
- سیستم گریس کاری اتومات برای دنده اصلی ،دنده پنیون و یاتاقان تنش زدایی شدن کل آسیاب بعد از جوشکاری
- *هدوال های ریخته گری
- قابلیت ساخت تا قطر 4متر و طول نامحدود
متغیرها در بال میل
تعدادی متغیر برای کنترل و در نظر گرفتن زمان استفاده از بال میل وجود دارد. از جمله این متغیرها:
متغیرهای میل
- قطر آسیاب
- سرعت چرخش
- درجه حرارت
متغیرهای توپ یا سنگ ریزه ها
- بار
- تراکم
- اندازه
- شکل
شارژ پایه میل
- حجم نسبی
- چسبندگی یا تغییر با گذر زمان
- تراکم
- نسبت ترکیب
سرعت چرخش در آسیاب گلوله ای از اهمیت بالایی برخوردار است و سه حالت اساسی عملیاتی برای آن وجود دارد که حرکت آبشاری گلوله ها را درون آسیاب گلوله ای نشان می دهد.
سه حالت در آسیاب گلوله ای اتفاق می افتد
- تفکیک کردن یا Centrifuging
- آب گلوله ای یا Cataracting
- آبشار یا Cascading
هنگامی که یک آسیاب به سرعت چرخانده می شود، موادی که درون بال میل یا آسیاب گلوله ای قرار دارد، مواد به وسیله نیروی گریز از مرکز به سمت خارج از بال میل رانده می شود. در این شرایط هیچ عمل فرسایشی برای بال میل رخ نمی دهد و کم کردن سرعت چرخش در بال میل ای باعث ایجاد چیزی شبیه به یک عمل کاتاراکتیو می شود که بسیار ناکارآمد خواهد بود. این کار منجر به فرسایش بیش از حد مواد می شود که باعث می شود مواد بیش از حد پراکنده شود.
در بال میل به 3 الی 7 برابر وزن پودر گلوله پر می شود که به طور موثر سنگ های معدنی و سرامیکی را آسیاب می کند. ماده ای که قرار است از آسیاب گلوله ای خارج شود باید به اندازه ای پودر شود که حفره های بین گلوله ها را پر کند. گلوله های با حرکت درون بال میل ،ذرات بزرگ مواد را با برخورد به یکدیگر و در یک راستا خورد می کنند و آنها را به نقطه شکست می رسانند.
کاربرد
به طور کلی، بال میل می تواند برای تولید محصولات خشک یا خیس به کار گرفته شود و قادر به تولید محصول در مقیاس میکرونیزه می باشد.
انواع بال میل
بال میل ها تجهیزات بسیار مفیدی برای سنگ زنی و خرد کردن به حساب می آیند. بال میل ها با توجه به امکاناتی که ارائه می دهند می توانند در انواع مختلفی به مشتریان ارائه شوند. انواع بال میل ها در زیر آمده است.
بال میل صنعتی
- این نوع آسیاب گلوله ای نسبت به دیگر بال آسیاب های گلوله ای بزرگتر می باشد.
- اندازه های آنها می تواند به اندازه یخچال و فریزر و یا اتوبوس باشد.
- تفاوت اصلی این آن با انواع دیگر در تعداد اتاقک های آنها است.
- سیستم هوا در این نوع اجباری است.
بال میل افقی
- نوع افقی شایع ترین نوعی است که در صنعت به کار می رود.
- بعضی از آسیاب های گلوله ای افقی مجهز به تایمر می باشند تا مواد را در دوره های زمانی مختلف بررسی کنند.
- می توان مواد پردازش شده موجود در آن را مشاهده نمود.
بال میل گرد
- این نوع اغلب برای کارهای آزمایشگاهی استفاده می شوند.
- این نوع برای برنامه های کوچک مناسب می باشند و در زمینه های آزمایشگاهی کاربرد دارند.
- در این نوع آسیاب های گلوله ای، گلوله ها را در اندازه های مختلف و برای کاربردهای مختلف، استفاده می شوند.
آسیاب های گلوله سال هاست که در کارخانه های فرآوری مواد معدنی فلزی و غیرفلزی مورد استفاده قرار می گیرند که احتمالاً در اولین مورد ذکر شده شیوع بیشتری داشته است. هدف اصلی کاهش اندازه به اندازه مناسب برای انجام فرآیند تغلیظ (فلوتاسیون، وزن سنجی یا مغناطیسی) و/یا شستشو (سیانور شدن کانی های حاوی طلا) است.
خوراکی که به آسیاب گلوله ای ارسال می شود محصول نهایی است که در مدار سنگ شکن به دست می آید، اندازه آن متغیر است زیرا به اندازه محصول نهایی آسیاب و به انرژی مورد نیاز آسیاب گلوله ای بستگی دارد. این بدان معنی است که خوراک نمی تواند خیلی درشت یا خیلی ریز باشد زیرا کیفیت محصول نهایی بر کارایی فرآیند بعدی تأثیر می گذارد. آسیاب معمولاً با افزودن آب و افزودن معرفهای شیمیایی مانند آهک برای تنظیم PH، کاهشدهندهها مانند سولفات روی و سیانید و برخی معرفها با ویژگیهای خاص بسته به ماده معدنی در حال فرآوری به عنوان مثال انجام میشود. ، افزودن جمع کننده های مولیبدنیت).
در داخل آسیاب گلوله ای باری از گلوله های فولادی وجود دارد که بین 30 تا 45 درصد حجم داخلی آسیاب را اشغال می کند. بار توپ ها می تواند از توپ هایی با قطر یکسان یا ترکیبی از اندازه های مختلف توپ تشکیل شود که امکان دستیابی به محصول نهایی مناسب را فراهم می کند. روابط ریاضی برای تعیین اندازه بهینه توپ های آسیاب وجود دارد و آنها بر اساس ویژگی های خاصی از مواد تغذیه می شوند، مانند وزن مخصوص، حداکثر اندازه و اندازه محصول نهایی. سطح داخلی بدنه استوانه ای آسیاب گلوله ای با آسترهای فولادی منگنزی پوشانده شده است، این آسترها دارای شکل سطحی متغیر و همچنین ضخامت آنها هستند که معمولی ترین آنها سطح موجدار است. طراحی لاینر مهم است زیرا اجازه می دهد بار به درستی بلند شود.
هنگامی که چرخش آسیاب گلوله ای شروع می شود، سنگ معدن، آب و محصولات شیمیایی در صورت لزوم وارد می شوند. در حین حرکت در داخل آسیاب، اختلاط دائمی بین محیط آسیاب (گلوله های فولادی) و سنگ معدن تولید می شود. همانطور که شارژ به سمت دهانه تخلیه آسیاب گلوله ای پیش می رود، کاهش اندازه انجام می شود. لازم به ذکر است که دو حرکت مهم در داخل آسیاب رخ می دهد، یکی آبشار و دیگری آب مروارید. در مورد اول، زمانی که توپها به بالاترین سطح خود میرسند، تمایل دارند روی توپها و باری که در سطح پایینتری قرار دارد بلغزند و حرکتی شبیه شکل خارجی کلیه ایجاد میکنند. در حرکت دوم، زمانی که توپها به بالاترین سطح خود میرسند، تمایل دارند از روی توپها بپرند و در سطح پایینتری بارگذاری کنند. در حالت اول، از آنجایی که تماس صمیمی و دائمی بین ذرات و گلوله ها وجود دارد، آسیاب و کاهش سایز بهتری ایجاد می شود، در حالی که در حالت دوم، به دلیل عدم تماس صمیمی، آسیاب کارایی چندانی ندارد. کنترل کافی جریان سنگ معدن و چگالی خمیر به حرکت مناسب بار در داخل آسیاب اجازه می دهد.
محصول از آسیاب گلوله ای در یک جعبه پمپ دریافت می شود و بسته به اندازه کارخانه تصفیه سنگ معدن و اندازه ذرات برای فرآیند، غلظت و/یا شستشو به سیستم اندازه گیری متشکل از یک یا چند سیکلون ارسال می شود. . سرریز سیکلون محصول نهایی است و تخلیه پایین حاوی ذرات درشتی است که باید برای آسیاب به آسیاب برگردانده شوند. چرخه سنگ زنی – طبقه بندی در طول عملیات تصفیه خانه مواد معدنی به طور مکرر تکرار می شود و کارایی آن بر فرآیند زیر (غلظت یا شستشو) تأثیر می گذارد.
آسیاب
اکثر آسیاب های تناژی امروزه در یکی از انواع تجهیزات زیر یا ترکیبی از دو یا چند آسیاب گلوله ای یا میله ای آسیاب می شود. آسیاب شیلی و هانتینگتون به صورت جداگانه استفاده می شوند.
آسیاب گلوله ای
همه انواع آسیاب ها اساساً از استوانه های دوار با ضلع های صاف یا مخروطی تشکیل شده اند و از گلوله های فولادی، میله های فولادی یا سنگریزه به عنوان رسانه آسیاب استفاده می کنند.
اصطلاح آسیاب گلوله ای به طور کلی برای اشاره به آسیاب استوانه ای که طول آن برابر یا بیشتر از قطر آن است استفاده می شود. در ابتدا برای سنگ زنی درشت توسعه داده شد، اما استفاده از آن در مدار بسته با طبقه بندی کننده، استفاده از آن برای آسیاب ریز گسترش یافته است.
آسیاب های گلوله ای پوسته ای از صفحات چدن یا فولاد دارند و روی ژورنال ها یا یاتاقان های توخالی حمل می شوند. سنگ معدن از طریق یک سطل، از نوع درام یا با یک فیدر در یک انتها تغذیه می شود و در قسمت مقابل تخلیه می شود.
آسیاب های گلوله ای را می توان به طور دلخواه به دو نوع تقسیم کرد که بستگی به روش تخلیه خمیر دارد. در آسیاب های سرریز یا سطح بالا که خمیر به سطح بالاتری می رسد تا زمانی که سرریز شود و از طریق ژورنال تخلیه شود. آسیاب های تخلیه بالا توسط تعداد زیادی از تولید کنندگان در سراسر جهان ساخته می شوند. آلیس چالمرز و میلز سطح پایین مارسی دارای یک رنده در نقطه تخلیه هستند. تخلیه با یک کوره نصب شده است. بین رنده و انتهای آسیاب بالابرهای شعاعی قرار دارند که به عنوان پمپی عمل می کنند تا تخلیه را از نقطه تخلیه یاتاقان یا تراننیون بالا ببرند. سیستم حرکت توسط سیستم دنده یا باند برای مدل های کوچک است.
آسیاب های گلوله ای در اندازه های مختلفی ساخته می شوند، از آسیاب های آزمایشگاهی کوچک تا حداکثر 12 فوت عرض و 12 فوت طول. دومی به حدود 1000 اسب بخار قدرت نیاز دارد. آسترها معمولاً از فولاد منگنزی، فولاد کروم یا چدن سفید با ضخامت 3 تا 6 اینچ هستند. معمولاً از ساختار بلند و موجدار برای افزایش عمل سنگ زنی استفاده می شود.
آسیاب توپ مخروطی
تفاوت آسیاب هاردینگ با اکثر آسیاب های گلوله ای در این است که انتهای مخروطی به قسمت استوانه ای آسیاب اضافه می شود. مخروط سمت تغذیه دارای زاویه باز بزرگتری نسبت به طرف مقابل است. سازندگان آن بیان میکنند که توپهای بزرگ در نزدیکی سمت غذا که ماده معدنی درشتتر وجود دارد متمرکز میشوند و در حالی که توپهای کوچکتر روی مواد معدنی ریزتر عمل میکنند.
آسیاب بار
آسیاب های میله ای از ابعاد کلی آسیاب های استوانه ای با قطرهای 3 تا 6 فوت و طول های دو تا سه برابر قطر آنها پیروی می کنند. آنها با آسیاب های گلوله ای تفاوت دارند زیرا میله های فولادی 3 یا 4 اینچ کوچکتر از طول آسیاب در داخل بین آسترها قرار دارند و به عنوان رسانه آسیاب استفاده می شوند. آسیاب های میله ای اغلب بر روی ژورنال ها و غلتک ها کار می کنند.
تخلیه سطح پایین در آسیاب میله ای مارسی با استفاده از یک حلقه حلقوی اریب دار در انتهای تخلیه به دست می آید. یک دروازه ثابت فولادی نزدیک به این حلقه قرار می گیرد و میله ها را در آسیاب نگه می دارد در حالی که خمیر کاغذ بین آسیاب و دروازه تخلیه می شود.
آستر آسیاب
تمام آسیاب های دوار باید دارای نوعی آستر قابل تعویض باشند. فولاد کروم، فولاد منگنز و چدن سفید عموماً به عنوان مصالح ساختمانی استفاده می شود. فرم هایی که برای ایجاد شکل موجدار یا مسطح به داخل آسیاب طراحی شده اند، اغلب برای جلوگیری از لغزش شارژ توپ استفاده می شوند. آسترهای جیبی نیز رایج هستند. این آسترها دارای جیب هایی هستند که توپ ها در آنها قرار می گیرند تا سطح پوشیدنی را تشکیل دهند.
آسترهای لاستیکی به صورت تجربی آزمایش شده اند اما به طور کامل توسط صنعت پذیرفته نشده اند. به گفته تاگارت، هیچ روش کاملاً رضایتبخشی برای نگهداشتن آسترها در محل ابداع نشد، کاربرد برای خوراکهای خوب و گلولههای کوچک محدود بود، ظرفیت آسیاب کوتاه شد، و در حالی که راندمان آسیاب کمی بالاتر در آزمایشهای مقایسهای با آسترهای فولادی نشان داده شد، هیچ روشی وجود نداشت. نشان می دهد که سایش روکش های لاستیکی هزینه بالاتر آنها را جبران می کند. گاهی اوقات از آسترهای سنگریزه به عنوان رسانه سنگ زنی در جایی که باید از آلودگی آهن اجتناب شود استفاده می شود.
تئوری سنگ زنی
آسیاب گلوله ای
آسیاب کردن در داخل آسیاب
سنگ زنی که در آسیاب هایی از این نوع انجام می شود معمولاً به دو عمل ضربه و ساییدگی نسبت داده می شود، اگرچه برخی از نویسندگان معتقد نیستند که بتوان بین این دو عمل مرزبندی کرد.
در آسیاب های میله ای یک خط تماس بین میله ها وجود دارد، آسیاب ضربه ای کمتری وجود دارد و عمل شبیه به غلتک است. در نتیجه، یک محصول آسیاب میله ای معمولاً حاوی درصد بالاتری در نزدیکی اندازه برش با محتوای ریزدانه کمتر از آسیاب گلوله ای است.
ظرفیت آسیاب
به طور کلی پذیرفته شده است که برای یک نوع سنگ، میزان آسیاب که می توان روی یک صفحه خاص توسط آسیاب گلوله ای یا میله ای بدست آورد به دو عامل بستگی دارد:
- اندازه رسانه آسیاب
- انرژی خالص عرضه شده به آسیاب.
در انتخاب رسانه آسیاب صحیح، مهم است که میلهها یا گلولههای عرضهشده اندازه کافی برای شکستن بزرگترین ذرات یک ماده معدنی در خوراک و بار کافی از گلولههای با اندازههای مختلف را داشته باشند، که میتوان آنها را در آسیابی که کار میکند پیدا کرد. برای مدتی، داشتن آسیاب بهتر از شارژ جدید.
با فرض اینکه رسانه آسیاب صحیح تعیین شده است، انرژی خالص را می توان با تغییر تغییر داد:
- وزن کل رسانه های آسیاب
- سرعت آسیاب
- اندازه دانلود
- درصد مواد جامد در خمیر
حجم شارژ حداکثر به حدود 50 درصد حجم آسیاب محدود می شود. اگر بار خیلی زیاد باشد، مرکز ثقل آن به محور آسیاب خیلی نزدیک می شود و قدرت تغذیه کاهش می یابد.
سرعت آسیاب با آنچه به عنوان “سرعت بحرانی” شناخته می شود، محدود می شود. این سرعتی است که در آن محموله شروع به چسبیدن به آسترها می کند یا شروع به چرخیدن می کند. با فرمول داده می شود.
N = 76.50/√d
N = دور در دقیقه
d = قطر داخلی بر حسب فوت
در عمل، سرعت مورد استفاده بسته به ترجیح اپراتورها و سازندگان، از 60 تا 80 درصد سرعت بحرانی متغیر است.
اندازه دهانه تخلیه بر مقدار خمیر باقی مانده در داخل آسیاب تنظیم می شود. حجم بسیار زیاد خمیر به دلیلی که قبلا ذکر شد، انرژی تغذیه شده را کاهش می دهد.
درصد جامدات در خمیر معمولاً در 60 تا 75 درصد نگه داشته می شود، اصل این است که درصد حجم جامدات را تا حد امکان بالا نگه دارید بدون از دست دادن تحرک محموله. نسبت صحیح آب به نوع ماده معدنی بستگی دارد، انواع کانی های لزج معمولاً به رقت بیشتری نسبت به مواد معدنی که دارای محتوای لجن پایین هستند نیاز دارند.
اندازه آسیاب مورد نیاز برای یک مشکل آسیاب خاص به شخصیت و اندازه خوراک و محصول مورد نظر و اینکه آیا آسیاب مدار باز یا بسته مورد نظر است بستگی دارد. تخمین دقیق ظرفیت فقط توسط یک مهندس آشنا با ارزیابی صحیح عوامل دخیل انجام می شود.
برای اهداف مرجع، جدول زیر ظرفیت آسیاب 48 و 100 مش را برای اندازه های مختلف آسیاب نشان می دهد. اسب بخار متصل نیز نمایش داده می شود. این ارقام برای یک کانی سیلیسی متوسط و برای بارهای نامی در گردش 2 یا 3 به 1 در نظر گرفته می شود.
این استعدادها را می توان در مورد سنگ معدن سخت و سخت که در برابر سنگ زنی بسیار مقاوم است تا 50 درصد کاهش داد و به همین دلیل پیشرفت های قابل توجهی در سال های اخیر روش هایی را برای تعیین قابلیت آسیاب شدن کانی های مختلف و همبستگی اطلاعات از آزمایشگاه با کارخانه های صنعتی FC Bond اطلاعات آسیابپذیری را بر اساس کار انجام شده توسط شرکت تولیدی آلیس-چالمرز و آزمایشهای آسیابپذیری آزمایشگاهی که بخشی از روش شرکت Dorr در وستپورت، کانن بوده است، منتشر کرده است.
مدار سنگ زنی باز و بسته بال میل
هنگامی که آسیاب گلوله ای برای اولین بار معرفی شد، آسیاب در یک مدار باز انجام می شد. سنگ معدن را آسیاب میکردند تا اندازه محدودی را از توری که فقط یک بار از آسیاب عبور میکرد عبور دهد. با این حال، مشخص شد که اگر زمان تماس کافی بین سنگ معدن و محیط آسیاب فراهم شود تا اطمینان حاصل شود که هیچ یک از ذرات آسیاب نشده (یا بزرگتر) از آسیاب خارج نمی شود، مقدار زیادی ریزدانه تولید می شود. به این معنی که سنگ معدن بسیار ریزتر از حد لازم آسیاب شد و ظرفیت آسیاب کاهش یافت.
مشکل با قرار دادن یک طبقه بندی در مدار برای جدا کردن مواد بزرگ از تخلیه آسیاب و بازگشت آن به آسیاب حل شد. در مدار بسته، نیازی به تکمیل آسیاب در یک گذر از آسیاب نیست، اما تمام تلاش می شود تا مواد با اندازه مناسب به محض تولید حذف شوند، بنابراین آسیاب بیش از حد کاهش می یابد و از ازدحام ریزدانه ها جلوگیری می شود. ذرات. به این ترتیب تناژی که یک آسیاب معین آسیاب می کند بیشتر از یک در مدار باز است.
با استفاده از یک طبقه بندی با ظرفیت بالا، بار گردشی می تواند 4:1 یا بیشتر باشد. نتیجه مستقیم افزایش ظرفیت، مصرف کمتر انرژی، آستر و رسانه آسیاب در هر تن سنگ معدن آسیاب شده است.
در عمل محدودیتی برای حمل بار در گردش وجود دارد. همانطور که ظرفیت ظاهراً بهبود می یابد، سرعت آسیاب کاهش می یابد، حرکت دادن حجم فزاینده مواد از طریق سیستم به تدریج دشوارتر می شود.
در ادبیات مربوط به نسبت بار گردشی اختلاف نظر وجود دارد. اصطلاحی که توسط اکثر اپراتورها استفاده می شود، نسبت تناژ شن برگشتی به آسیاب به خوراک اصلی است.
اگر طبقهبندی مدار به جای آسیاب تغذیه شود، مواد درشت حاوی بیش از اندازه خوراک اصلی و بیشاندازه تخلیه است که تعریف چندان دقیقی نیست.
بار گردشی را می توان با آنالیز مش با استفاده از فرمول های زیر محاسبه کرد:
- زمانی که سنگ معدن مستقیما وارد آسیاب می شود:
بار گردشی = d – o/s – d
d = درصد انباشته تخلیه نسبت به یک مش
o = درصد تجمعی مش یکسان در سرریز طبقه بندی کننده
s = درصد انباشته شده از مش مشابه در دبی درشت طبقه بندی کننده
- هنگامی که سنگ معدن وارد طبقه بندی کننده می شود:
بار گردشی = f – o/s – d
f = درصد انباشته یک مش در خوراک d، s، o، در 1 نشان داده شده است.
روش معمول این است که از این فرمول ها برای محاسبه بار گردشی برای اندازه های مختلف استفاده کنید و باری را که خارج از مقادیر ظاهر می شود دور بریزید و سپس میانگین را بگیرید.
نمودارهای بال میل جریان سنگ زنی
امروزه انواع مختلفی از فلوچارت ها استفاده می شود. روند در آسیاب های جدید خرد کردن نسبتاً خوب (¾ تا ½ اینچ) است. آسیاب های گلوله ای مدار بسته تک مرحله ای با طبقه بندی کننده ها برای آسیاب های درشت تر از مش 48 مناسب هستند، اما زمانی که محصول ریزتر است، آسیاب های گلوله ای مدار بسته دو مرحله ای با طبقه بندی معمولی هستند. راندمان لزوماً باید تا حدی در کارخانههای کوچک قربانی هزینه سرمایه شود و حتی نسبتهای کاهش بزرگتر در مرحله آسیاب توجیه میشوند.
با طبقهبندیکنندههای بزرگ که برای تحمل بارهای در گردش بالا استفاده میشوند، اغلب لازم است از یک دستگاه کمکی برای تکمیل حلقه بسته استفاده شود. در برخی موارد از یک سطل موتوری برای بلند کردن خمیر تخلیه شده به طبقهبندی کننده استفاده شده است.
آسیاب های میله ای برای آسیاب درشت استفاده می شود و روند فعلی استفاده از آنها در مدارهای باز برای مرحله اول آسیاب است.
آسیاب مرحله ای در آمریکای شمالی اغلب با آسیاب های گلوله ای به عنوان مرحله اول و آسیاب های بزرگتر برای مرحله دوم انجام می شود.
سنگ زنی توپ
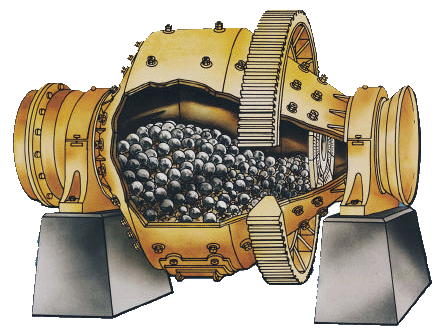
آسیاب گلوله ای نوعی آسیاب است که برای آسیاب و مخلوط کردن مواد برای استفاده در فرآیندهای اختلاط مواد معدنی، رنگ ها، پیروتکنیک ها، سرامیک ها و تف جوشی لیزری انتخابی استفاده می شود. این بر اساس اصل ضربه و اصطکاک کار می کند: کاهش اندازه زمانی حاصل می شود که رسانه های سنگ زنی مشخصه این تجهیزات (گلوله ها یا کره ها) بر روی یکدیگر و در برابر ذرات ماده ای که قرار است تکه تکه شود، برخورد کنند.
از یک ظرف استوانه ای تشکیل شده است که حول محور خود می چرخد. محور استوانه می تواند افقی باشد یا زاویه کمی با افقی داشته باشد. سیلندر تا حدی با توپ هایی پر شده است که می تواند از فولاد (فولاد کروم)، فولاد ضد زنگ، سرامیک هایی مانند کاربید سیلیکون یا حتی لاستیک ساخته شود. سطح داخلی سیلندر معمولاً با مواد مقاوم در برابر سایش مانند کاربید سیلیکون، فولاد منگنز یا لاستیک پوشیده شده است. طول آسیاب تقریبا برابر با قطر آن است.
عواملی که می توانند بر سنگ زنی تأثیر بگذارند:
- سرعت چرخش (دور در دقیقه، دور در دقیقه). بر این اساس اندازه (قطر داخلی) کوزه تعیین می شود. اگر موادی که قرار است آسیاب شوند بسیار چسبناک هستند، به ماشینی نیاز دارد که کنترل سرعت داشته باشد، اما پایدار نباشد. سپس برای کنترل مشکل نیمی از موادی که معمولاً با آب بیشتری استفاده می شود اضافه می شود. این مشکل در کائولن ها و رس ها رخ می دهد. سرعت بحرانی جایی است که نیروی گریز از مرکز عمل میکند و با «چسباندن» مواد و توپها به دیوارههای شیشه بدون افتادن، از آسیاب کردن جلوگیری میکند.
- تعداد توپ ها آنها معمولا از آلومینا، سیلیس و حتی فلز ساخته می شوند. توپ ها باید بین 30 تا 55 درصد از حجم داخلی ژاکت را اشغال کنند. اندازه و وزن توپ باید ثابت بماند وگرنه حجم آن تغییر می کند. سایش تا حد زیادی بر تغییر حجم تأثیر می گذارد، سایش باید برای تراز کردن محتوای توپ ها، اضافه کردن توپ های جدید و از بین بردن توپ های فرسوده کنترل شود.
- اندازه و شکل توپ . دو عامل را باید در نظر گرفت: سطح تماسی که با آن زمین میشود، توپهای کوچکتر از این نظر بهتر هستند و حرکتی که به دو شکل است. یکی که در آن توپ ها به دور یکدیگر می چرخند و می لغزند، و دیگری که در آن توپ ها از یکدیگر دور می شوند، در این مرحله توپ های بزرگ بهتر هستند. باید بین هر دو عامل تعادل پیدا کرد. سنگ چخماق (سنگ چخماق) را می توان استفاده کرد، قبل از استفاده آنها را برای حذف ناخالصی های آلی کلسینه می کنند. سنگ چخماق تقریباً 100٪ سیلیس است، از این رو سختی بالایی دارد. توپ های خمیری را می توان از چینی، چینی با آلومینا بالا، چینی زیرکونیا تهیه کرد، اما در مورد دومی باید در نظر داشته باشید که توپ ها سریعتر فرسوده می شوند. برای آسیاب کردن توپ های ریزتر مورد نیاز است. لازم است توپ ها را به صورت دوره ای بررسی کنید، زمانی که سایش بسیار بالایی دارند حذف می شوند زیرا توپ های جدید آنها را آسیاب می کنند و ترکیب آسیاب را تغییر می دهند.
- مقدار مواد . مقدار مواد و سیال همیشه مرتبط است زیرا ویسکوزیته را تعیین می کند، ویسکوزیته حرکت توپ ها را کنترل می کند. اگر مایع کمی وجود داشته باشد، توپها به سختی حرکت میکنند و اگر مایع اضافی وجود داشته باشد، توپها میپرند و از پایین و دیوارههای آستر پریده و زود فرسوده میشوند. صدای تولید شده توسط توپ ها باید ثابت باشد، اگر صدا وجود نداشته باشد، سنگ زنی وجود ندارد.
- دانه بندی مواد.
- زمان عملیات . هرچه سختی ماده مورد آسیاب بیشتر باشد، زمان بیشتری برای رسیدن به دانه بندی خاص نیاز است، با در نظر گرفتن اینکه هر چه زمان عملیات طولانی تر باشد، مصرف انرژی و در نتیجه هزینه عملیات بیشتر می شود. ویسکوزیته ماده نیز باید برای محاسبه زمان عملیات در نظر گرفته شود، زیرا اگر نوعی حلال در مخلوط یافت شود، می تواند متفاوت باشد.
آسیاب گلوله ای BICO BOND 395-50 بال میل
تجهیزات آسیاب طراحی شده توسط FC Bond برای تعیین شاخص آسیاب مواد معدنی. دارای یک شمارنده رگرسیون دیجیتال است که به طور خودکار موتور آن را متوقف می کند. یک دکمه حرکت دستی که به شما امکان می دهد آن را در موقعیت مناسب برای تخلیه قرار دهید. عملکرد چرخش آن حداکثر 70 دور در دقیقه است.
تجهیزات شامل:
- 44.5 پوند بار توپ های آهنی:
- 25 توپ 1-1/2 اینچی
- 39 توپ 1-1/4 اینچی
- 60 توپ 1 اینچی
- 68 توپ 7/8 اینچی
- 93 توپ 3/4 اینچی
- پایه فلزی
- سینی دریافت
- سینی پر کردن
- درام چرخشی 12×12 اینچی
همچنین ممکن است به موارد زیر علاقه مند باشید: شکن
میز غلتکی
ایده آل برای اجرای آزمایشات در آسیاب زغال سنگ و/یا گلوله/میله.
مشخصات:
- ظرفیت رول از 2 تا 16 رول
- ارتفاع استاندارد 32 اینچ
- ساخت PTR 2×2 اینچی
- صفحه گیج 10
- موتور 1/2 اسب بخار (از 2-4 غلتک) و 1 اسب بخار (از 4 غلتک به بعد).
- موتور سه فاز یا تک فاز
- انتقال متغیر از 20-240 دور در دقیقه (از 2-4 غلتک) و از 0-80 دور در دقیقه (از 4 غلتک به بعد).
- دکمه توقف اضطراری
- غلتک طول 5 اینچ x 24 اینچ.
بدون الزام با یکی از مدیران ما مشورت کنید تا اطلاعات بیشتری در مورد آسیاب و میز غلتک به دست آورید.
تیم | شرح |
---|---|
EP5004 | آسیاب توپی/میله ای رومیزی فولادی سخت شده 8 اینچ |
EP5003 | آسیاب توپی/میله ای میز فولادی سخت شده 8 اینچ 8 اینچ 8 اینچ 10 |
تیم | شرح |
---|---|
EP80001N | 2 میز غلتکی برای آسیاب توپ، 42 “X30” X32 اینچ، گیربکس 1/2 اسب بخار، 220 ولت، 3PH، 60 دور در دقیقه متغیر |
EP80002N | میز 3 غلتکی برای آسیاب توپ، گیربکس 42 اینچ 30 اینچ X32، گیربکس 1/2 اسب بخار، 220 ولت، 3PH، متغیر 60 دور در دقیقه |
EP80003N | میز 3 غلتکی برای آسیاب توپ، موتور گیربکس 1/2 اسب بخار، 47 اینچ X30 اینچ X32، 220 ولت، 3PH، متغیر 60 دور در دقیقه |
EP80004N | 4 میز غلتکی برای آسیاب توپ، 56 اینچ X37 اینچ X32، موتور کاهنده 1 اسب بخار، 220 ولت، 3PH، 1500 دور در دقیقه متغیر |
EP80005N | میز با 8 غلتک در 2 سطح، 56 اینچ X37 اینچ X32، موتور کاهنده 1 اسب بخار، 220 ولت، 3PH، 1500 دور در دقیقه متغیر |
آسیاب گلوله ای یک دستگاه افقی است که دارای نصب چرخشی لوله ای شکل است که آن را به مهم ترین تجهیزات پس از خرد کردن مواد تبدیل می کند.
آسیاب های گلوله ای نسبت به آسیاب های دیگر محصول ظریف تری را در فرآیند آسیاب ارائه می دهند زیرا عمل آسیاب توسط ذرات سنگ معدن درشت تر که بین میله و میله درون یابی شده اند کند می شود. این آسیاب ها در یک مدار بسته با طبقه بندی چنگک، مارپیچ یا هیدروسیکلون کار می کنند.
این آسیابهای گلولهای توسط یک درایو تسمه V و چرخ دندههای محرک یا کاهش دهنده هدایت میشوند.
آسیاب های گلوله ای را می توان بر اساس دنده طبقه بندی کرد:
- آسیاب توپ دسته ای
- آسیاب گلوله ای در حال اجرا مداوم
تعداد گلوله های قرار داده شده در داخل آسیاب به میزان انرژی موجود برای حرکت آسیاب بستگی دارد.
آسیاب گلوله ای به طور گسترده در موارد زیر استفاده می شود:
- مزارع سیمان
- ساخت و ساز
- مواد نسوز
- کودهای شیمیایی
- معدن
- تولید سفال
کوچک و موثر
آسیاب های گلوله ای موثرترین آسیاب های آزمایشگاهی برای آسیاب سریع دسته ای تا بهترین اندازه ذرات نمونه های سخت، نرم، چسبناک، رشته ای، حساس به دما و مرطوب هستند. مواد آسیاب شده توسط ضربه و اصطکاک بین توپ های سنگ زنی و دیواره داخلی کاسه سنگ زنی یا ملات پردازش می شود.
سنگ زنی را می توان به صورت خشک یا مرطوب انجام داد. آسیاب های گلوله ای علاوه بر آسیاب، کمکی ایده آل و قابل اعتماد در آزمایشگاه برای اختلاط و همگن سازی هستند. برای جلوگیری از سایش آزاردهنده، مجموعه های سنگ زنی ساخته شده از بسیاری از مواد مختلف در دسترس هستند.
آسیاب گلوله ای و آسیاب غلتکی
کاهش دما و بهینه سازی فرآیندها در آسیاب.
حرارت دادن در طول فرآیند آسیاب می تواند کیفیت مواد زمین را کاهش دهد. از طریق تزریق آب به آسیاب گلوله ای، حرارت اضافی دفع می شود و دمای خروجی در سطح مورد نظر حفظ می شود. تنها در صورتی که بتوان از افزایش دما به طور قابل اطمینانی جلوگیری کرد، می توان مواد خام آسیاب شده یا سیمان آسیاب شده را به طور ایمن و کارآمد حمل و ذخیره کرد. در مورد آسیاب های غلتکی، بستر آسیاب با تزریق مایع تثبیت می شود و در نتیجه فرآیند آسیاب بهینه می شود.
راه حل ما
ما معمولاً یک یا دو سیستم تزریق مایع را توصیه می کنیم که به صورت اختیاری مجهز به پین های چرخشی برای لنج ها هستند.
محصولات بال میل
لنج های تزریق و سیستم های خنک کننده
خنک کننده و تهویه کارآمد
لچلر لنج ها و سیستم های نازل برای تولید محدوده اندازه قطرات بهینه و توزیع آن تا حد امکان به طور یکنواخت در جریان گاز.
آسیاب های گلوله ای فردی: از سال 1864 ادغام شده است
صدها آسیاب گلوله ای با نام تجاری فایفر، توزیع شده در سرتاسر جهان، به صورت جداگانه برای مشتری: کارمندان Gebr. Pfeiffer SE بیش از صد سال است که در حال ساخت، تولید و مونتاژ آسیاب های گلوله ای است. آسیاب گلوله ای همچنین برای پردازش محصولات سخت که به ویژه فرسوده می شوند عالی است.
اصل کار
محصول آسیاب از طریق یک یا هر دو ژورنال وارد آسیاب می شود و توسط بدنه های آسیاب ضربه ای و اصطکاکی خرد می شود. محصول آسیاب از طریق شکاف تخلیه در لوله آسیاب، از طریق دیواره تخلیه یا سرریز از طریق پین های انتهایی، محفظه سنگ زنی را ترک می کند. اجرا و تنظیم شکاف تخلیه یا دیواره تخلیه بر ترکیب دانه محصولات تأثیر می گذارد. در آسیاب مدار بسته، ظرافت محصول را می توان در جداکننده تنظیم کرد یا در مورد سنگ زنی درشت با دستگاه جداکننده پایین دست، اندازه مش جداکننده را می توان از قبل انتخاب کرد.
داده های تکنیکی | |
---|---|
جریان تا | تا 50 تن در ساعت |
اندازه خوراک | تا 30 میلی متر |
ظرافت نهایی | تا 10 میکرومتر |
ماده ای که باید درمان شود | هیدرات آهک |
آسیاب میله و توپ
شرح
Eral-Chile آسیابهای میلهای و گلولهای لولهای کوچک و متوسط را تولید میکند که آسیابهای گلولهای با قدرت بزرگ یا آسیابهای SAG را در کارنامه خود ندارد.
آسیاب ها از یک فرول ساخته شده از ورق فولادی ضخیم، جوشکاری مکانیکی، با انتهای چدنی تشکیل شده است که توسط فلنج هایی با استفاده از پیچ و مهره های با استحکام بالا به فرول ثابت می شود. هم فلنج های فرول و هم فلنج های قطعات انتهایی ماشین کاری می شوند تا از تراز کامل پوسته آسیاب اطمینان حاصل شود.
داخل فرول یا با پوشش های فولادی آلیاژی یا با لاستیک محافظت می شود. در مورد آسیاب های میله ای معمولاً روکش های فولادی روی دیواره های سر نصب می شود تا از پاره شدن لاستیک توسط میله ها جلوگیری شود.
محرک معمولی آسیاب ها با استفاده از یک مجموعه پینیون-تاج است. در آسیاب های کوچک، با قدرت محرک تا 250 کیلو وات، مجموعه پینیون تاج با استفاده از دندانه های مستقیم بریده می شود، در حالی که در قدرت های بالاتر، از چرخ دنده هایی با دندانه های پروفیل مارپیچ یا شاه ماهی استفاده می شود.
در توان تا 250 کیلو وات (آسیاب های 2.0 mx 4.0 m، 7 ft x 14 ft) آسیاب ها را می توان مستقیماً با استفاده از سیستم های الکترونیکی راه اندازی کرد و در نهایت می تواند با استفاده از یک کلاچ پنوماتیکی که به طور خودکار فعال می شود، راه اندازی را وارد کند.
سیستم روانکاری مونتاژ تاج پینیون از طریق پاشش کنترل شده گریس و هوا انجام می شود. تکیه گاه های اصلی آسیاب و همچنین یاتاقان های شفت پینیون با گریس و به طور کامل اتوماتیک ساخته می شوند.
Eral-Chile آسیابهای لولهای تا قطر 3 متر (10 فوت) را تولید میکند که روی یاتاقانها پشتیبانی میشوند، اما این آسیابها مستقل از محور پینیون روغن کاری میشوند.
برای ظرفیتهای کوچک، Eral-Chile آسیابهایی با قطر تا 1.5 متر تولید میکند که فرول آنها بر روی چرخهای بانداژی قرار میگیرد که در همان زمان که آسیاب را پشتیبانی میکنند، حرکت چرخشی به آن میدهند. این آسیاب ها دارای حداکثر قدرت درایو 75 کیلو وات هستند و به صورت گلوله ای و میله ای تولید می شوند.
عملکرد بال میل
آسیاب های میله ای برای آسیاب های متوسط تا 1 میلی متر مناسب هستند و می توانند محصولات خوراک تا 15 میلی متر را دریافت کنند. نسبت طول به قطر در حد 1.5 است و حداکثر طول معمولاً حدود 6.5 متر است.
حجم پرکردن آسیاب های میله ای معمولاً دسی لیتر 35 درصد است، اگرچه گاهی اوقات می توان آنها را تا 45 درصد پر کرد. توان بزرگترین آسیاب های میله ای بین 1500 کیلو وات تا 2000 کیلووات است.
آسیاب های گلوله ای برای دریافت محصولات خوراک کوچکتر از 1-2 میلی متر مناسب هستند و محصولاتی را معمولاً کوچکتر از 0.5 میلی متر با محتوای بالای ذرات کوچکتر از 0.074 میلی متر (200 مش) تحویل می دهند. درجه پر شدن نرمال آسیاب های گلوله ای 40٪ است، اگرچه آنها می توانند به مقادیر 45٪ نیز برسند.
میلگردهای مورد استفاده در آسیاب ها دارای طول کمی کمتر از طول آسیاب و قطر میلگردها حداکثر 125 میلی متر و حداقل قطر آن 25 میلی متر است. آنها فولاد آهنگری هستند
قطر توپ ها از 25 میلی متر تا 150 میلی متر است، اگرچه این گلوله های بزرگ فقط در آسیاب های بسیار بزرگ و ترجیحاً در آسیاب های SAG استفاده می شوند. گلوله های چدنی و فولادی آهنگری وجود دارد، اما بدون شک گلوله های دوم به دلیل عمر طولانی تر سایش و مقاومت در برابر شکستگی بیشترین استفاده را دارند.
برنامه های کاربردی
آسیاب های میله ای عمدتاً به عنوان مراحل آسیاب اولیه و سپس مرحله آسیاب ثانویه با آسیاب های گلوله ای استفاده می شوند.
آسیاب های میله ای اغلب در فرآیندهای وزن سنجی استفاده می شوند تا از تولید ریزدانه های زیادی که بعداً در فرآیندهای غلظت از بین می روند جلوگیری شود. میل آسیاب برای تولید آسیاب های صاف ایده آل است.
بیشترین کاربرد آسیاب های گلوله ای در آسیاب مس، طلا، کانی های چند فلزی و سنگ آهن است.
آسیاب های گلوله ای به طور گسترده در آسیاب یا میکرونیزه کردن سیلیس و کربنات کلسیم برای تولید محصولات سیمان الیافی استفاده می شود که در آن آسیاب های بسیار ریز در حد 80% <38 میکرون مورد نیاز است که معادل حدود 5000-6000 Blaine است. این مدارهای آسیاب ریز سیلیس مرطوب هستند و یک مدار بسته با هیدروسیکلون ها ایجاد می کنند. Eral-Chile دارای تجربه گسترده ای در این نوع مدارهای سنگ زنی است که چندین سال است که در آمریکای لاتین و سایر کشورها فعالیت می کند.
با درود و تشکر از زحمات برای جمع آوری مطالب پیشنهاد ام این است برای درک بهتر مطالب تا حد ممکن برای نام تجهیزات و ابزار و پروسه های کاری از اصطلاحات رایج در صنعت استفاده شود تا مطالب گویا تر باشند استفاده از نامهای غیر متعارف که صرفا ترجمه انگلیسی کلمات بوده برای خواننده مبهم و گیج کننده میباشد .با احترام یوسفی