دوزینگ پمپ سلنوئیدی حجم تزریقی کمتری دارد و کاربری و هوش بهتری نسبت به پمپ دوزینگ موتوری دارد.
دوزینگ پمپ سلنوئیدی دارای مگنت می باشند. با ورود جریان برق، این مگنت دارای بار الکتریکی شده و توسط میدان مغناطیسی بوجود آمده شفت فلزی را به حرکت در می آورد و با قطع و وصل شدن جریان، شفت با یک فنر به عقب رانده می شود. این شفت متصل به دیافراگم یا پیستون بوده و به این روش عملیات مکش و تزریق انجام می گردد.
https://maharfanabzar.com/download/prominent/PM-Operation-Solenoid.pdf
سلونوئید یک فنر پیچ خورده درون یک بستهٔ محکم ماریپیچیست. در فیزیک، سلونوئید یک حلقهای از سیم است که اغلب دور یک هستهٔ فلزی پیچیده شده. وقتی یک شدت جریان به آن متصل شود باعث بوجود آمدن یک میدان مغناطیسی میشود.
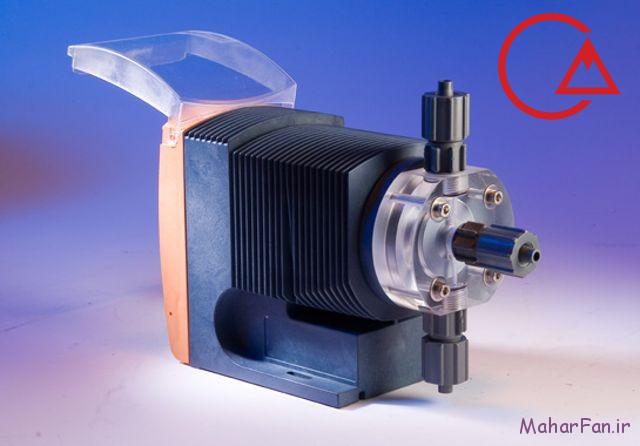
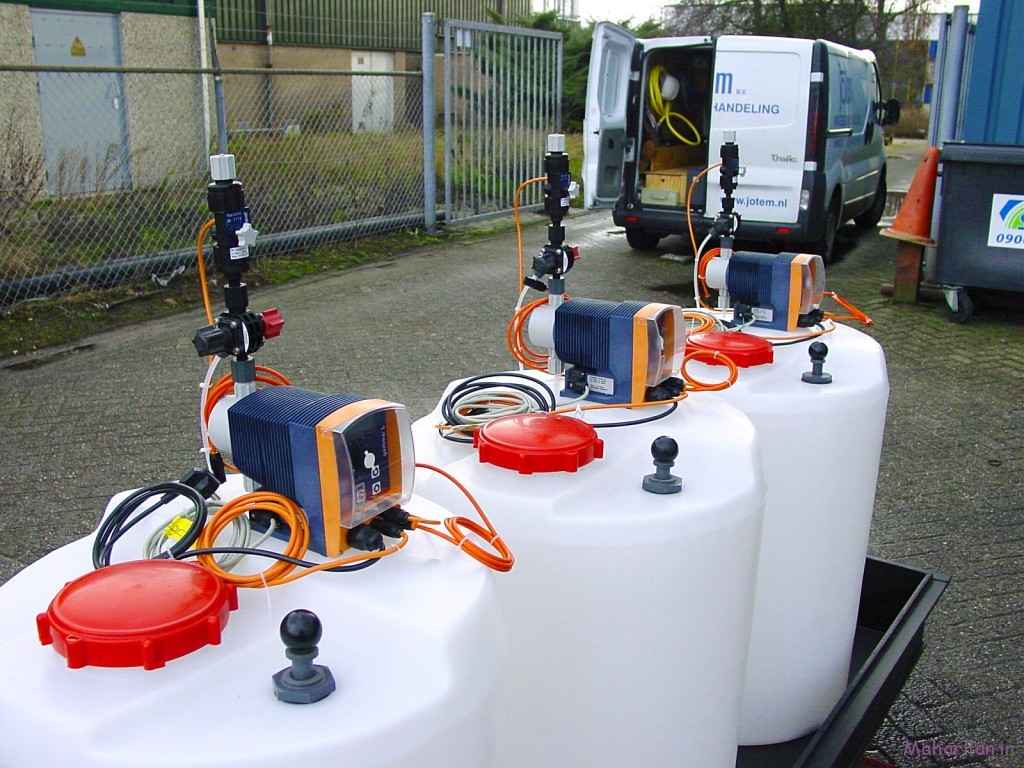
سلونوئیدها بسیار مهم اند چون میتوانند یک میدان مغناطیسی کنترل شده بوجود آورند و یا همچنین میتوانند به عنوان یک آهن ربا مورد استفاده قرار بگیرند.
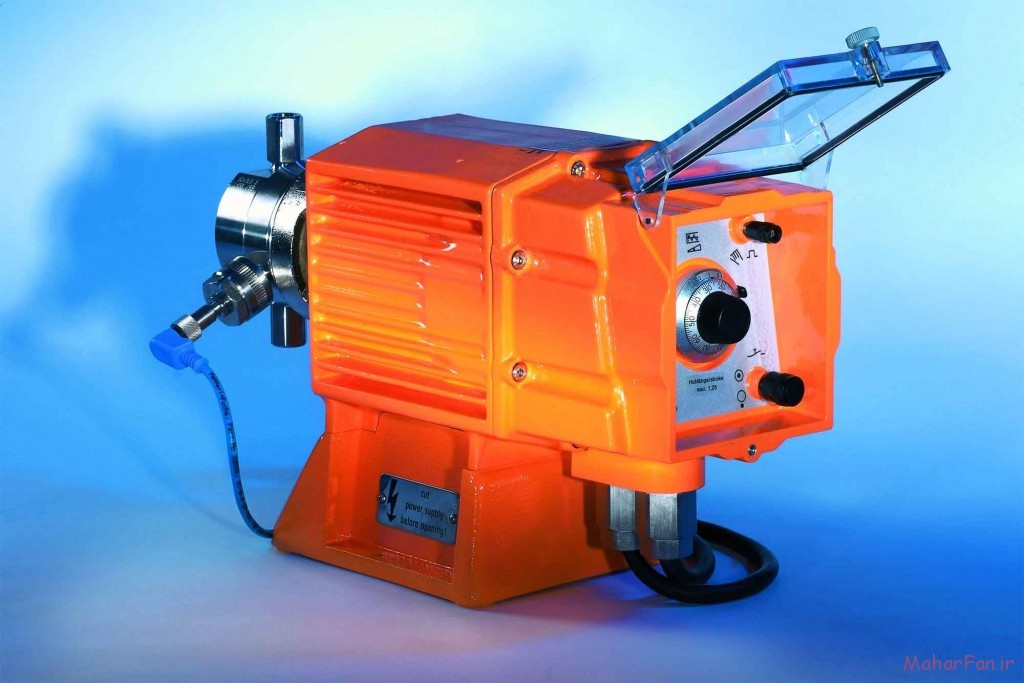
در مهندسی، سلونوئید به عنوان یکی از انواع گوناگون ترانسفورماتورهایی که انرژی را به حرکت خطی تبدیل میکنند
مورد استفاده قرار میگیرند. همچنین سلونوئید اغلب بعنوان یک سوپاپ مغناطیسی نیز مورد استفاده قرار میگیرند
که یک وسیلهٔ مکمل از سلونوئید برقی-مکانیکی است
که سوپاپهای بادی و هیدرولیکی یا یک کلید مغناطیسی (دستگاه تقویت کننده ایست که از داخل از یک سنولوئید استفاده میکند) را فعال کند. به عنوان مثال:
سلونوئید استارتر ماشین
یک سنولوئید برقی (یک سلونوئید برقی-مکانیکی است)
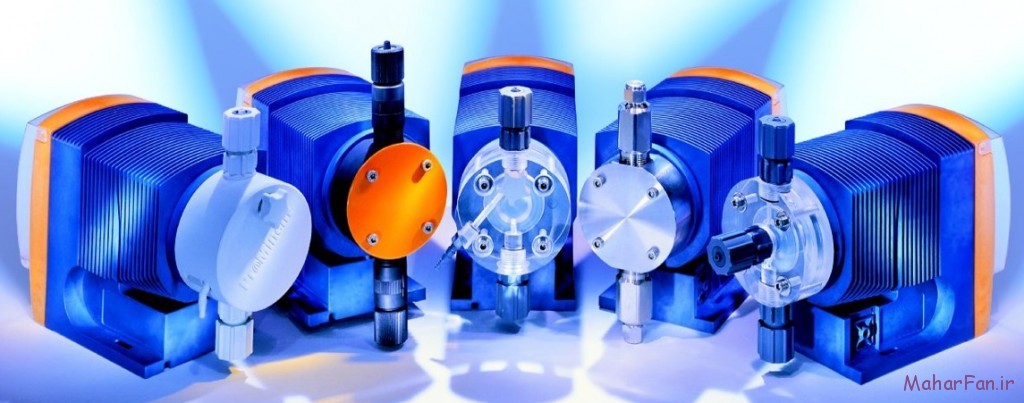
-
پمپ تزریق خود مکش
اطلاعات بیشتر -
شیر تزریق (Injection valve)
4,500,000تومان افزودن به سبد خرید -
فوت ولو یا شیر مکش (Foot valve)
اطلاعات بیشتر -
دوزینگ پمپ آلدوز ALLDOS
اطلاعات بیشتر -
پمپ تزریق جریانی دوزاترون 10 درصدی d3re10
9,000,000تومان افزودن به سبد خرید -
شیر اطمینان فشار متغیر دوزینگ سویجلاک swagelok
15,000,000تومان افزودن به سبد خرید -
شیر تزریق فنردار دوزینگ
900,000تومان افزودن به سبد خرید -
شیر تزریق فنردار دوزینگ
3,400,000تومان افزودن به سبد خرید -
پمپ تزریق 120 لیتربرساعت 4 بار PVDF
78,300,000تومان افزودن به سبد خرید